How to Choose the Right Phosphating Agent for Your Needs
2025-06-18
How to Choose the Right Phosphating Agent for Your Needs
Table of Contents
1. Introduction to Phosphating Agents
2. Understanding Phosphating and Its Importance
3. Types of Phosphating Agents
3.1 Zinc Phosphating
3.2 Manganese Phosphating
3.3 Iron Phosphating
4. Factors to Consider When Choosing a Phosphating Agent
5. Appli
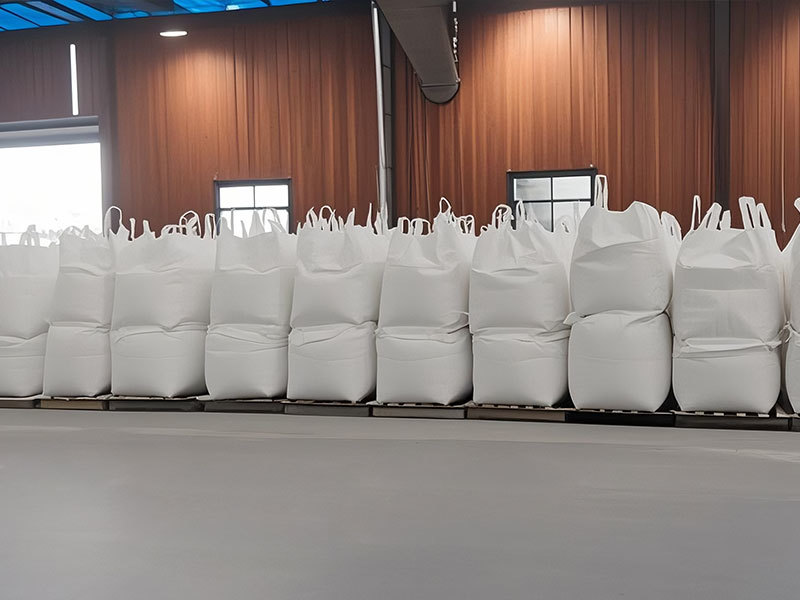
How to Choose the Right Phosphating Agent for Your Needs
Table of Contents
- 1. Introduction to Phosphating Agents
- 2. Understanding Phosphating and Its Importance
- 3. Types of Phosphating Agents
- 4. Factors to Consider When Choosing a Phosphating Agent
- 5. Applications of Phosphating Agents in Industry
- 6. Environmental Considerations in Phosphating
- 7. The Phosphating Process: A Step-by-Step Guide
- 8. Conclusion
- 9. FAQs
1. Introduction to Phosphating Agents
Phosphating agents play a crucial role in various industrial processes, particularly in the metal treatment sector. These compounds create a protective phosphate coating on metal surfaces, enhancing their corrosion resistance and providing a suitable surface for subsequent coatings. Understanding the right phosphating agent for your specific needs is essential for achieving optimal results in your applications.
2. Understanding Phosphating and Its Importance
Phosphating is a chemical process that involves the application of a phosphate conversion coating on metal substrates. This treatment serves multiple purposes, including improving adhesion for paints and coatings, enhancing corrosion protection, and reducing friction. The **importance of phosphating** cannot be understated, particularly in industries where metal components are exposed to harsh environments.
The quality of the phosphate coating directly impacts the durability and longevity of the final product. Therefore, selecting the appropriate phosphating agent tailored to your specific requirements is essential for achieving the best performance.
3. Types of Phosphating Agents
When it comes to phosphating agents, several types are available, each with its unique properties and applications. Selecting the right type is critical for optimal performance.
3.1 Zinc Phosphating
Zinc phosphating is one of the most commonly used methods due to its excellent corrosion resistance and good adhesion properties. The process involves the application of a zinc phosphate coating, which is particularly effective in protecting steel and iron substrates. Zinc phosphating can be utilized in various industries, including automotive, aerospace, and general manufacturing.
3.2 Manganese Phosphating
Manganese phosphating offers superior wear resistance compared to zinc phosphating and is often used for components subjected to high friction. This phosphating agent is commonly found in the aerospace industry, military applications, and other sectors that require enhanced performance under stress. The coating provides excellent lubrication properties, making it ideal for parts such as gears and machinery components.
3.3 Iron Phosphating
Iron phosphating is a cost-effective option for protecting ferrous metals. While it may not offer the same level of corrosion resistance as zinc or manganese phosphating, it is still a viable choice for applications where cost is a primary concern. This method is often used in the appliance and electronics industries, providing a good surface for painting and coating.
4. Factors to Consider When Choosing a Phosphating Agent
Selecting the right phosphating agent involves considering several factors that can influence performance and efficacy. These include:
4.1 Substrate Material
Different metal substrates respond differently to phosphating agents. Understanding the type of metal you are working with is crucial. For instance, zinc phosphating works exceptionally well with steel, while iron phosphating is better suited for ferrous metals.
4.2 Application Method
The method of application can also affect the choice of phosphating agent. Whether you are using spray, immersion, or brush application will impact the thickness and uniformity of the coating.
4.3 Environmental Conditions
Consider where the treated metal will be used. For environments with high humidity or exposure to chemicals, a more robust phosphating agent may be necessary to ensure lasting protection.
4.4 Compliance and Regulations
Different industries have specific regulations regarding the use of chemical agents. Ensure that the phosphating agent you choose complies with local and international safety and environmental regulations.
5. Applications of Phosphating Agents in Industry
Phosphating agents find applications across various sectors, each with unique requirements:
5.1 Automotive Industry
In the automotive industry, phosphating is used to protect metal components from rust and corrosion, ensuring the longevity and reliability of vehicles.
5.2 Aerospace Industry
The aerospace sector demands high-performance coatings. Manganese phosphating is often employed to provide enhanced wear resistance for critical components.
5.3 Electronics
In electronics, iron phosphating is used to prepare metal surfaces for painting and coating, improving aesthetic appeal and protecting against corrosion.
6. Environmental Considerations in Phosphating
In today’s world, environmental sustainability is more important than ever. Companies must choose phosphating agents that minimize environmental impact while still delivering performance. Look for agents that are free from harmful chemicals and those that meet environmental compliance standards.
7. The Phosphating Process: A Step-by-Step Guide
Understanding the phosphating process can help you select the right agent and apply it correctly. Here’s a step-by-step guide:
7.1 Surface Preparation
Begin by thoroughly cleaning the metal surface to remove oils, dirt, and rust. This step ensures better adhesion of the phosphating agent.
7.2 Application of Phosphating Agent
Apply the chosen phosphating agent using the selected method (spray, immersion, or brush). Ensure even coverage for optimal results.
7.3 Curing
Allow the coating to cure as per the manufacturer’s instructions. Curing time may vary based on the type of agent used.
7.4 Quality Inspection
Conduct a quality inspection to ensure the coating meets the required thickness and uniformity standards.
8. Conclusion
Choosing the right phosphating agent is a critical decision that can significantly impact the performance and longevity of metal components. By understanding the different types of phosphating agents, considering key factors, and following the correct application process, you can ensure optimal results for your specific needs. The right phosphating agent will not only enhance corrosion resistance but also improve the overall aesthetics and functionality of your products.
9. FAQs
1. What is a phosphating agent?
A phosphating agent is a chemical compound used to create a phosphate conversion coating on metal surfaces, improving corrosion resistance and surface properties.
2. What are the different types of phosphating agents?
The main types of phosphating agents include zinc phosphating, manganese phosphating, and iron phosphating, each with unique properties and applications.
3. How do I choose the right phosphating agent?
Consider factors such as substrate material, application method, environmental conditions, and compliance with regulations when selecting a phosphating agent.
4. Can phosphating agents be used on non-ferrous metals?
Yes, while most phosphating agents are designed for ferrous metals, some formulations can be adapted for non-ferrous metals as well.
5. What is the environmental impact of phosphating agents?
The environmental impact varies by agent. It is essential to choose phosphating agents that comply with safety and environmental standards to minimize their ecological footprint.