Exploring Different Types of Phosphating Agents and Their Applications
2025-06-28
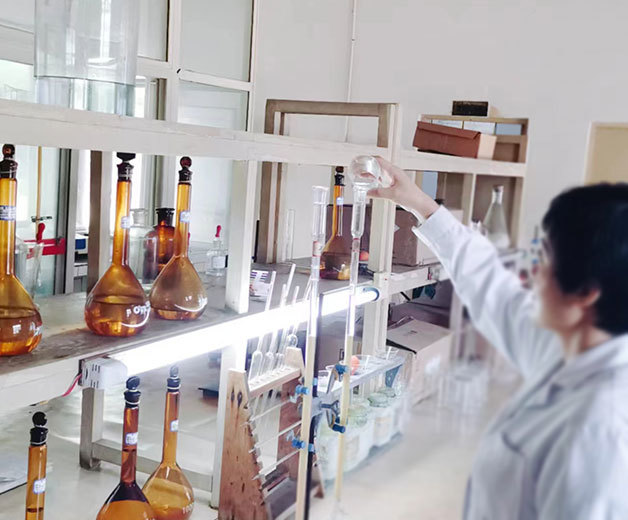
Exploring Different Types of Phosphating Agents and Their Applications
Phosphating agents play a crucial role in various industrial applications, particularly in surface treatment processes. These agents are primarily used to protect metal surfaces from corrosion, enhance adhesion for paints and coatings, and improve overall durability. In this detailed exploration, we will discuss the different types of phosphating agents, their compositions, applications, advantages, and evolving trends in the industry.
Table of Contents
- 1. Introduction to Phosphating Agents
- 2. Types of Phosphating Agents
- 3. Mechanism of Action of Phosphating Agents
- 4. Applications of Phosphating Agents
- 5. Advantages of Using Phosphating Agents
- 6. Best Practices in Phosphating Processes
- 7. Future Trends in Phosphating Technology
- 8. Frequently Asked Questions
- 9. Conclusion
1. Introduction to Phosphating Agents
Phosphating agents are chemical substances that facilitate the formation of phosphate coatings on metal surfaces. These coatings are typically formed through a chemical reaction between the phosphating agent and the metal surface, resulting in a protective layer that enhances corrosion resistance and prepares the surface for subsequent treatments. Given their critical role in various industries, understanding the different types of phosphating agents and their specific uses is paramount.
2. Types of Phosphating Agents
Phosphating agents can be classified based on their chemical composition and the specific type of metal they are designed to treat. Here, we will discuss the three primary types of phosphating agents.
2.1 Zinc Phosphating
Zinc phosphating is one of the most widely used phosphating processes. It involves applying a solution that contains zinc phosphate, resulting in a corrosion-resistant layer on steel and iron surfaces. This type of phosphating is particularly beneficial for applications where metal components are exposed to harsh environmental conditions. The zinc layer aids in rust prevention and improves paint adhesion, making it a preferred choice in automotive and construction industries.
2.2 Manganese Phosphating
Manganese phosphating is another significant type of phosphating agent. It is primarily used for its excellent wear resistance attributes. The manganese phosphate coating provides a porous structure that can retain lubricants, making it ideal for components subjected to friction, such as gears and bearings. This type of phosphating is commonly utilized in the aerospace and military sectors due to its durability and performance under extreme conditions.
2.3 Iron Phosphating
Iron phosphating involves creating a phosphate coating using iron phosphates. While it offers moderate corrosion protection compared to zinc and manganese phosphating, it is often employed as a pre-treatment for painting and coating applications. This type of phosphating is cost-effective and widely used in the manufacturing of appliances and machinery, where aesthetic appeal and paint adhesion are of paramount importance.
3. Mechanism of Action of Phosphating Agents
Understanding how phosphating agents work is essential for optimizing their use. The mechanism typically involves a reaction known as phosphatization, where the phosphating solution interacts with the metallic substrate. This chemical reaction leads to the formation of a crystalline layer of metal phosphate, which adheres strongly to the substrate.
During this process, the following key actions occur:
1. **Surface Preparation**: The metal surface is cleaned to remove any contaminants, ensuring effective bonding with the phosphating agent.
2. **Chemical Reaction**: The phosphating solution reacts with the metal ions, leading to the formation of a stable phosphate compound on the surface.
3. **Coating Formation**: The resultant phosphate coating provides a protective barrier that enhances corrosion resistance and prepares the surface for additional treatments.
4. Applications of Phosphating Agents
Phosphating agents find applications across various industries due to their versatile properties. Below are some key sectors where phosphating plays a critical role.
4.1 Automotive Industry
In the automotive sector, phosphating is extensively used for surface treatment of various components. Zinc phosphating, in particular, is favored for its exceptional corrosion resistance, making it ideal for parts that are exposed to moisture and harsh weather conditions. Phosphated surfaces also provide excellent paint adhesion, which is crucial for achieving a durable finish on vehicles.
4.2 Aerospace Industry
The aerospace industry requires components that can withstand extreme conditions, making manganese phosphating an excellent choice. The wear-resistant properties of manganese phosphate coatings enhance the durability of aerospace parts, contributing to the overall safety and performance of aircraft. Additionally, phosphating helps in reducing friction, thus improving fuel efficiency.
4.3 Electronics Industry
In the electronics sector, phosphating agents are used to treat metal components such as connectors and housings. Iron phosphating is commonly employed as a pre-treatment for painting electronic parts, ensuring better adhesion and protection from corrosion. This application is crucial for extending the lifespan of electronic devices, particularly those exposed to varying environmental conditions.
5. Advantages of Using Phosphating Agents
The use of phosphating agents offers several advantages, making them a preferred choice in many industrial applications. Below are some key benefits:
1. **Corrosion Resistance**: Phosphate coatings provide a robust barrier against corrosion, significantly extending the lifespan of metal components.
2. **Enhanced Adhesion**: The porous structure of phosphate coatings improves adhesion for paints and coatings, leading to better aesthetics and durability.
3. **Cost-Effectiveness**: Phosphating processes are relatively cost-effective compared to other surface treatment methods, providing a good return on investment.
4. **Versatility**: Different types of phosphating agents cater to various industries and applications, making them a versatile choice for manufacturers.
5. **Environmental Compliance**: Many phosphating processes are compliant with environmental regulations, providing a safer option for manufacturers.
6. Best Practices in Phosphating Processes
To maximize the effectiveness of phosphating agents, it is essential to follow best practices in the phosphating process. Below are some recommended practices:
1. **Surface Preparation**: Ensure thorough cleaning of metal surfaces to remove grease, dirt, and oxides before applying phosphating agents.
2. **Control of Process Parameters**: Monitor factors such as temperature, concentration, and pH levels during the phosphating process to achieve optimal results.
3. **Post-Treatment Rinsing**: After phosphating, rinse the components to remove any excess chemicals, preventing contamination of subsequent treatments.
4. **Quality Control**: Implement stringent quality control measures to assess the thickness and adhesion of phosphate coatings, ensuring compliance with industry standards.
7. Future Trends in Phosphating Technology
As industries evolve, so do the technologies surrounding phosphating agents. Key trends to watch include:
1. **Eco-Friendly Phosphating Solutions**: There is a growing demand for environmentally friendly phosphating alternatives that reduce the use of hazardous chemicals.
2. **Innovative Coating Technologies**: Research is underway to develop advanced phosphating solutions that enhance performance while minimizing environmental impact.
3. **Automation and Efficiency**: The integration of automation in phosphating processes is streamlining operations, improving efficiency, and reducing production costs.
8. Frequently Asked Questions
**Q1: What is the primary purpose of phosphating agents?**
A1: The primary purpose of phosphating agents is to create a protective phosphate coating on metal surfaces to enhance corrosion resistance and improve paint adhesion.
**Q2: How long does the phosphating process typically take?**
A2: The phosphating process duration can vary depending on the method used and the desired coating thickness, typically ranging from a few minutes to several hours.
**Q3: Are phosphating agents environmentally friendly?**
A3: Many traditional phosphating agents contain hazardous chemicals; however, there is a growing trend towards developing eco-friendly alternatives that comply with environmental regulations.
**Q4: Can phosphating be applied to non-metallic surfaces?**
A4: Phosphating is primarily used on metallic surfaces; however, some specialized processes may extend to specific non-metallic materials.
**Q5: What are the common industries that utilize phosphating agents?**
A5: Common industries include automotive, aerospace, electronics, and manufacturing, where metal components are frequently used.
9. Conclusion
Phosphating agents are indispensable in modern industrial applications, providing crucial benefits such as corrosion protection and enhanced adhesion. By understanding the different types of phosphating agents and their specific applications, manufacturers can make informed decisions that significantly improve the quality and longevity of their products. As we look towards the future, ongoing advancements in phosphating technology promise to deliver even more efficient and environmentally friendly solutions, further solidifying the role of phosphating agents in various industries.